Wall Systems in Prefabricated Houses
Wall systems in prefabricated houses play an important role in the structural integrity and energy efficiency of the house. These systems require a different approach from traditional methods. Wall systems of prefabricated houses are generally created using modular panels.
Wall systems in prefabricated houses should be selected by taking into account important factors such as insulation, energy saving, durability and sound insulation. Each system has certain advantages and should be preferred in accordance with the requirements of the project. Wall systems are a critical element for the comfort and durability of the prefabricated house, and it is important to make the right choice.
The panels not only provide protection against external factors, but also provide heat, sound and water insulation.
The walls of prefabricated houses with good quality materials and production offer reliable usage advantages. Commonly used panel systems include press panels and carcass panels. In this production method, fibercement material is preferred on the surfaces. The main function of these walls is to provide insulation.
Wall systems frequently used in prefabricated houses are as follows:
Press Panel
Fibercement+EPS+Fibercement) and Carcass Panel (Fibercement+Rockwool+Fibercement)
Standard pressed panel is the most economical panel form. As standard, the outer wall thickness is 100 mm and the inner wall thickness is 60 mm. Internal wall thickness can be made to 100 mm upon customer request. The surfaces of the outer and inner panels are made of fibercement board with dimensions of 8x1250x2500 mm. For thermal insulation, 84 mm polystyrene rigid foam (EPS) is used between the panels on the outer wall and 44 mm on the inner walls. 8 mm thick fibercement sheets are adhered by pressing method on special adhesives applied to both surfaces of the EPS insulation.
Depending on preference and need, instead of a pressed panel, a carcass panel can be made by screwing fibercement to both surfaces of the steel carcass skeleton. When a carcass panel is preferred, the insulation material is rockwool (14 kg/m³). The biggest advantage of the carcass panel is that, together with the rockwool insulation material, it gives the wall A1 class fire resistance.
The outer surfaces of pressed and carcass panels are painted directly on the surface without the need for any extra processing. A double coat of acrylic exterior paint is recommended here. On interior surfaces, paint is applied directly to the surface without the need for any extra processing.
Galvanized steel H profiles, which connect the walls and also have load-bearing properties, appear on the exterior and interior surfaces.
Those who do not want to see H profiles on the interior wall can optionally have plasterboard panel covering. After plasterboard coating, satin plaster and mesh should be applied to the joints before painting.
In prefabricated buildings; manufacturing is done with roll-forming machines. The special profiles that make up the structure; With the automatic profile line, all necessary forms are created and the necessary installation and connection gaps are made completely under computer control. No welding is used during the manufacturing and assembly phase. Joints are made with bolts and/or screws of special standards.
Fluted Panel
(Fluted Fibercement+EPS+Fibercement)
Another option, fluted panels whose design and patent belongs to our Nestavilla brand, is preferred in residential and multi-purpose buildings where aesthetics are prioritized. Horizontal lines are created with the fibercement on the outer surface of the panel, which adds an aesthetic appearance to the facades. Optionally, it can be made as pressed or carcass panel. When a carcass panel is preferred, the insulation material is rockwool (14 kg/m³).
These panels offer a more aesthetic appearance on the exterior parts of prefabricated structures. As standard, the outer wall thickness is 100 mm and the inner wall thickness is 60 mm. Internal wall thicknesses can be increased to 100 mm if desired.
For thermal insulation, 82 mm outside and 44 mm inside polystyrene rigid foam (EPS) is used between these panels. Fibercement boards measuring 8x1250x2500 mm are glued to both surfaces of the insulation material with special adhesives.
On the exterior, all galvanized steel H profiles, which also have load-bearing properties, are covered with fibercement slats. This process prevents the formation of thermal bridges and keeps the heat inside. Fibercement jambs are applied to all window and exterior door edges. This adds visual aesthetics to the structure.
Paint is applied directly to the surface without the need for any extra treatment on the outer surface. Double coat of acrylic exterior paint is recommended.
Paint is applied also directly to the interior surface without the need for any extra treatment.
Galvanized steel H profiles, which also have a carrier feature, are visible on the inner surface.
For those who do not want to see H profiles on the interior wall, optional plasterboard panel covering can be done. After plasterboard coating, satin plaster and mesh should be applied to the joints before painting.
Manufacturing in our prefabricated buildings is done with rollforming machines. All necessary forms are created with the automatic profile line of the profiles that make up the structure, and the necessary installation and connection spaces are made completely under computer control. No welding is used during the manufacturing and assembly phase. Joints are made with bolts and/or screws of special standards.
Advantages of Fluted Panel System:
- There are wall thickness alternatives suitable for all kinds of climate zones.
- Since the wall panels do not require a profile carcass, no thermal bridges occur.
- Since the materials are shipped with a special packaging system, no damage occurs during shipping and handling.
- It saves time on the construction site with its quick installation feature.
- It has the feature of being disassembled and reassembled many times.
The wall systems generally preferred in corporate prefabricated buildings are as follows;
The sheet metal in roll entering the panel production line is first given the desired form by the "rollforming" process. Then, panels are created using insulation materials such as EPS or rockwool between the formed sheets. Panels are automatically cut to the desired dimensions, packaged and made ready for shipment.
Press Panel
(Fibercement+EPS+Fibercement)
The pressed panel is produced in the factory, transported to the construction site and assembled quickly. These panels are used to speed up the construction process and reduce labor costs. Prefabricated buildings, built faster and more economically with the fibercement panel system, have multiple installation and disassembly features.
Since the wall panels do not require a profile carcass, no thermal bridges occur. Both sides of the walls of pressed panel buildings are fibercement. EPS is used as insulation material. Fibercement boards are glued to both sides of EPS.
Using press panels in the construction of prefabricated buildings offers a faster construction process than traditional methods and also requires less labor.
Carcass Panel
(Fibercement+(Carcass+Rockwool)+Fibercement)
Fibercement is used on both sides of the walls of carcass panel buildings. After using EPS or rockwool as insulation material according to the customers' needs, the fibercements are screwed to the special profile carcass.
Prefabricated buildings, built faster, more economic and also have multiple installation and disassembly features.
Rockwool (14 kg/m³) is used as insulation material in carcass panels. The biggest advantage of the carcass panel is that, together with the rockwool insulation material, it gives the wall A1 class fire resistance. Paint is applied directly to the surface without the need for any extra treatment on the outer surface. A double coat of acrylic exterior paint is recommended here.
Composite Panel
(Sheet + (EPS or Rockwool) + Fibercement)
One side of the composite panel is produced as sheet metal and the other side as fibercement. EPS or rockwool is used as insulation material in the composite panel. While EPS offers a more economical solution, rockwool is both more resistant to burning with its A1 class non-flammability feature and is much more advantageous in reaching high insulation values. The outer surfaces of the composite panel enter production painted. Only the interior walls need to be painted at the construction site. Composite panels are preferred in the construction of buildings used for purposes such as offices, dormitories, dining halls, WC-showers, affordable housing and social facilities on construction sites. Prefabricated buildings, built faster, more economic and also have multiple installation and disassembly features.
Sandwich Panel
(Sheet+(EPS or Rockwool)+Sheet)
Sandwich panel is a system that can protect structures against external factors and offers practical and economical solutions for an extremely strong stance. Sandwich panels; provide a modern look with their light, durable structure.
Both surfaces of the sandwich panel are sheet metal and EPS or rockwool is used as insulation material. While EPS offers a more economical solution, rockwool is more resistant to burning with its A1 class non-flammability feature and is much more advantageous in reaching high insulation values. The Neopan technology we have developed provides a significant cost advantage by eliminating the painting process on the construction site that needs to be applied to exterior facades. Because both sheet metal surfaces of the sandwich panel go into production painted and are packaged as such. Sandwich panels are preferred in the construction of buildings used for purposes such as offices, dormitories, dining halls, WC-showers, affordable housing and social facilities on construction sites. It can also be used to cover the roof facades of buildings or to obtain cold storages.
Carcass Composite Panel
(Trapezoidal Printed Sheet+(EPS+Rockwool)+Fibercement)
These panels generally consist of two main components:
External surface coating: This layer is made of galvanized sheet material with trapezoidal section. This material increases the panel's resistance to external influences and provides a decorative appearance.
While EPS or polystyrene foam is generally used as an insulation material, Vekon recommends rockwool as an insulation material here. These insulation materials also provide thermal insulation and fire resistance.
Advantages of Carcass Composite Panel:
Thermal insulation: Thanks to the insulation layer, it increases energy efficiency and minimizes heat losses.
Lightness: These panels generally have a lightweight structure, making the construction process easier.
Aesthetics: Provides a decorative exterior with various color and pattern options.
Durability: Exterior coating protects the panels against external influences and ensures their long life.
Roof Details
Trusses used on the roofs of prefabricated buildings and cleadings floors between floors of multi-storey buildings are produced with our Profacto technology, completely weldless and with bolt connections.
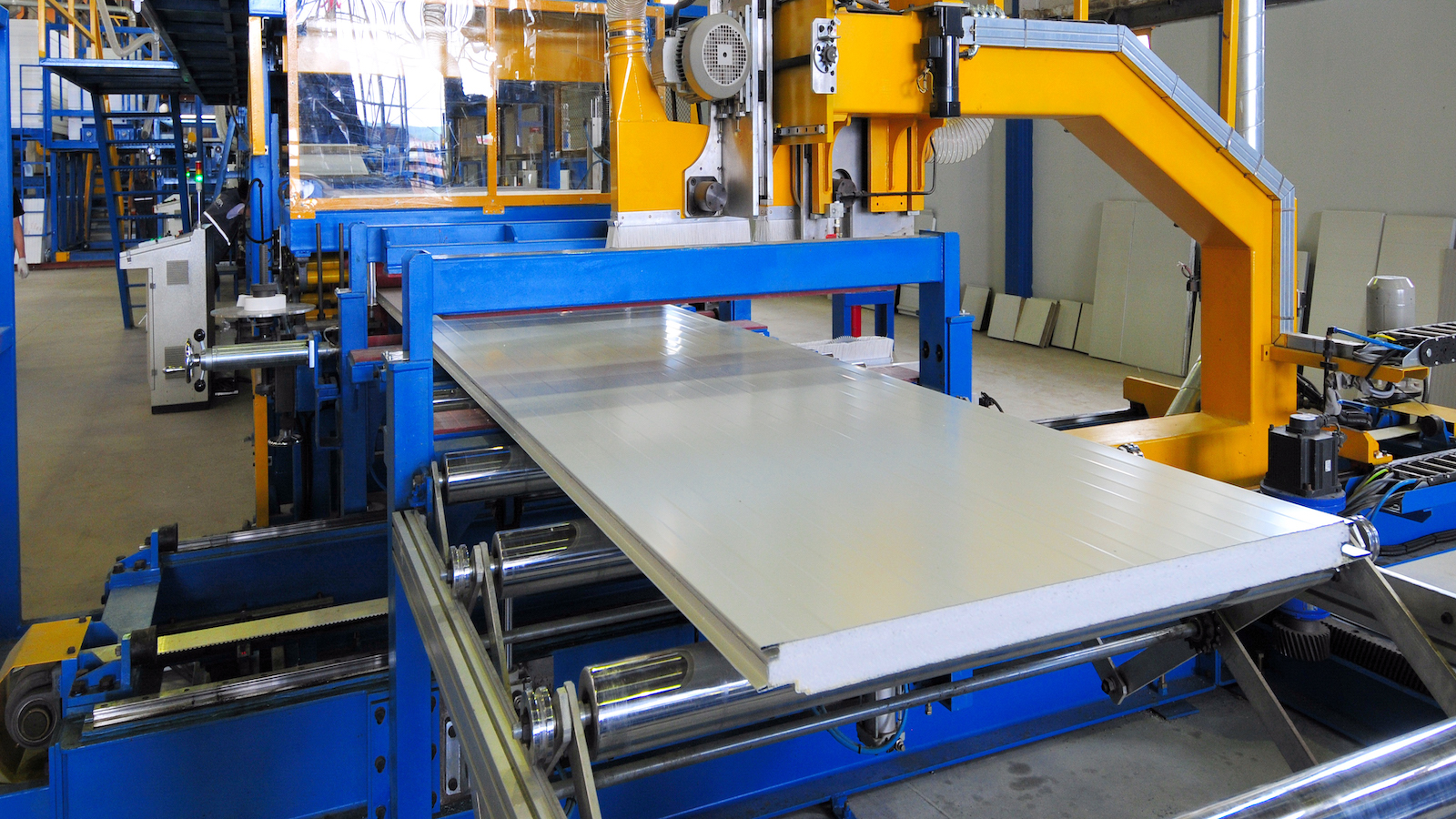